Biodiesel Production
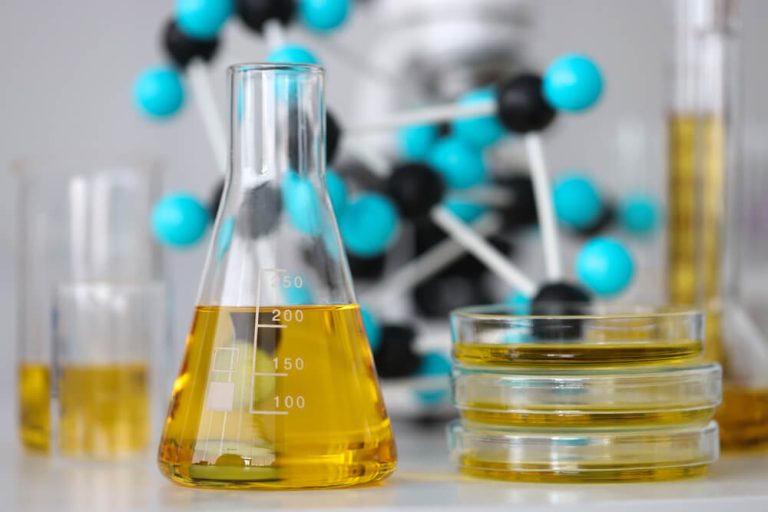
Biodiesel Production
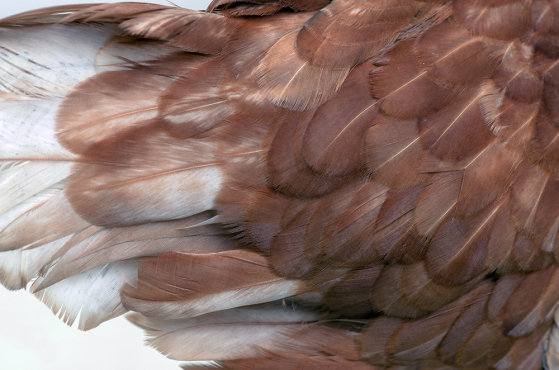
Waste Fat to Fuel
Through our biodiesel plant, we convert rendered poultry fat into biodiesel, reducing dependency on fossil fuels and contributing to a cleaner, greener future.
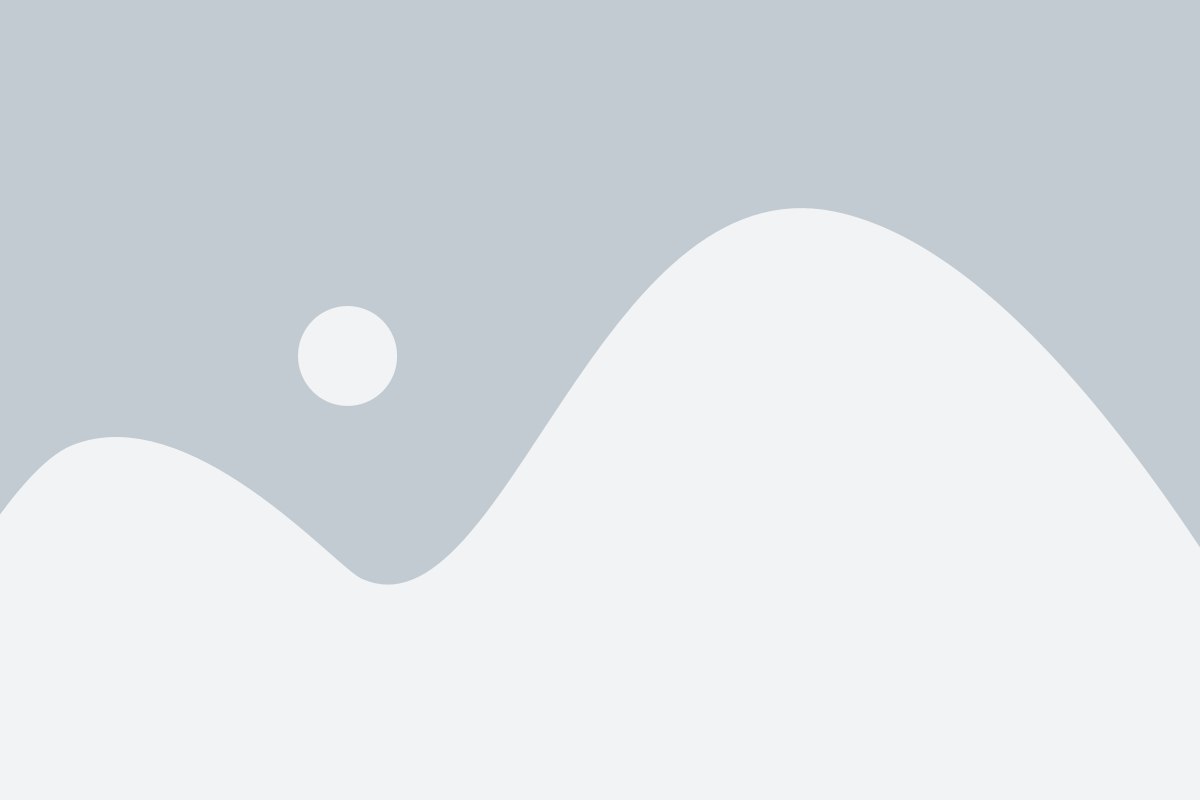
Renewable Energy Source
Our biodiesel is a low-carbon alternative to conventional diesel, offering an eco-friendly solution for industries and businesses looking to reduce their carbon footprint.
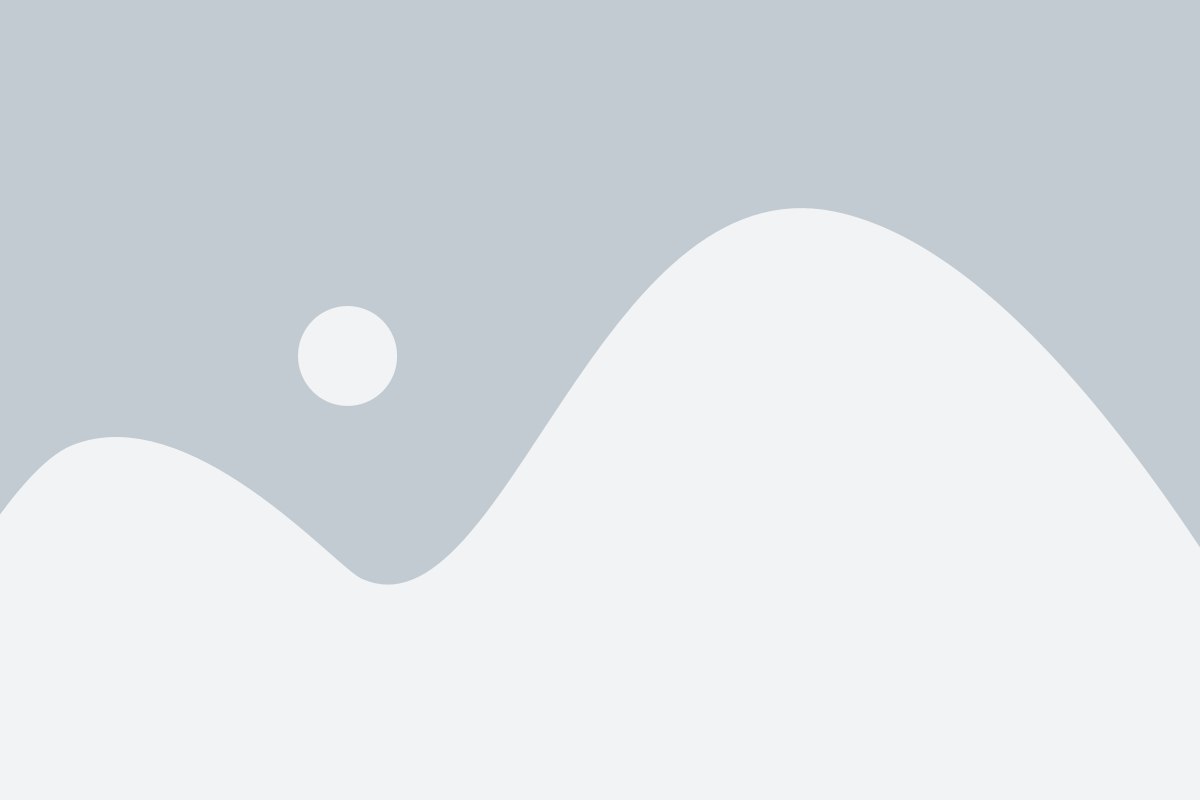
Sustainable Practices
We follow the strictest environmental regulations to ensure that our biodiesel production is energy-efficient, minimizes waste, and contributes to a sustainable, circular economy.
Industries We Serve
Serving Diverse Industries with Sustainable Products
We provide essential products for a wide range of industries, all produced from poultry waste and waste fats. By partnering with us, industries can meet their sustainability goals while benefiting from high-quality materials.
Animal Feed
Our rendered protein meals and feather meal provide essential nutrients for animal feed, supporting livestock and poultry industries with sustainable feed ingredients.
Agriculture
We supply protein meals and blood meal for use in fertilizers that enrich soil and promote healthy crop growth, contributing to sustainable agricultural practices.
Renewable Energy
Our biodiesel fuels industrial machinery, vehicles, and other heavy-duty equipment, providing a clean, renewable alternative to conventional diesel.
Industrial Applications
Our rendered tallow is used in various industrial processes, including soap production, lubricants, and bio-based materials.